Twin Screw Extruder as a Continuous Chemical Reactor
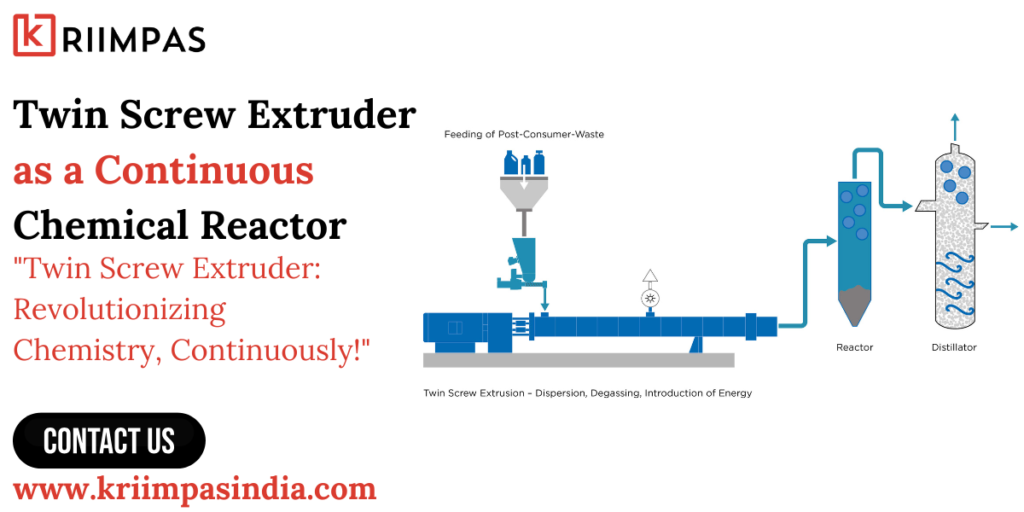
Twin Screw Extruder/Twin Screw Extruder as a Continuous Chemical Reactor/Twin Screw Extruder Machines as a Continuous Chemical Reactor/Twin Screw Extruder Machines Provider/Twin Screw Extruder Machines Dealer/
Table of Contents
Introduction
Welcome to Kriimpas India Pvt. Ltd., where we offer comprehensive solutions for all your material processing needs. Since 2012, we have been dedicated to providing top-notch machinery and services to our valued customers. We are the best Provider of Twin Screw Extruder as a Continuous Chemical Reactor.
Our range of offerings includes Processing Machinery for different Materials, Motion Based Solutions, Automation & Technological Solutions, Additive & Hybrid Manufacturing Solutions, and a wide array of spares and parts. Each product is meticulously engineered using the latest technology and premium quality raw materials sourced from reliable vendors. Our commitment to excellence ensures that our products meet stringent industry standards, delivering exceptional quality and performance.
Did you know that the twin screw extruder (TSE), which is used extensively in the plastics industry to process a variety of materials, can also function as a continuous chemical reactor? This multipurpose device can carry out a number of tasks, such as mixing, compounding, and polymerisation. The idea of employing a twin screw extruder machine as a continuous chemical reactor will be addressed in detail in this blog, along with the benefits, uses, and special advantages Kriimpas India Pvt. Ltd. provides in this area.
What is a Twin Screw Extruder (TSE)?
To process materials, a twin screw extruder uses two intermeshing screws that rotate inside a barrel. Although melting and shaping materials—particularly polymers—is a TSE’s primary function, the machine has developed into something much more. The TSE can function as a continuous chemical reactor where different chemical processes take place in a controlled and effective manner by employing a particular design and configuration.
Extruders are traditionally used to melt and shape thermoplastic materials, but they are now also used in a wider range of industries, such as chemical processing, food processing, and pharmaceuticals.
How Does a Twin Screw Extruder Act as a Continuous Chemical Reactor?
Raw materials go through a number of reactions in a typical chemical reactor that alter their chemical makeup. The purpose of a chemical reactor is to heat, mix, and occasionally promote materials to create the desired result. Similar tasks are carried out continuously by the twin screw extruder when it is utilised as a chemical reactor.
Because the TSE is continuous, it is very effective for large-scale production because raw materials can be continuously fed into the system and products can be continuously extruded. In addition to applying heat and shear forces to promote chemical reactions, the intermeshing screws aid in the mixing and transportation of the materials. Controlled reactions are made possible by a TSE’s precise temperature and pressure control, which is crucial in a variety of industries.
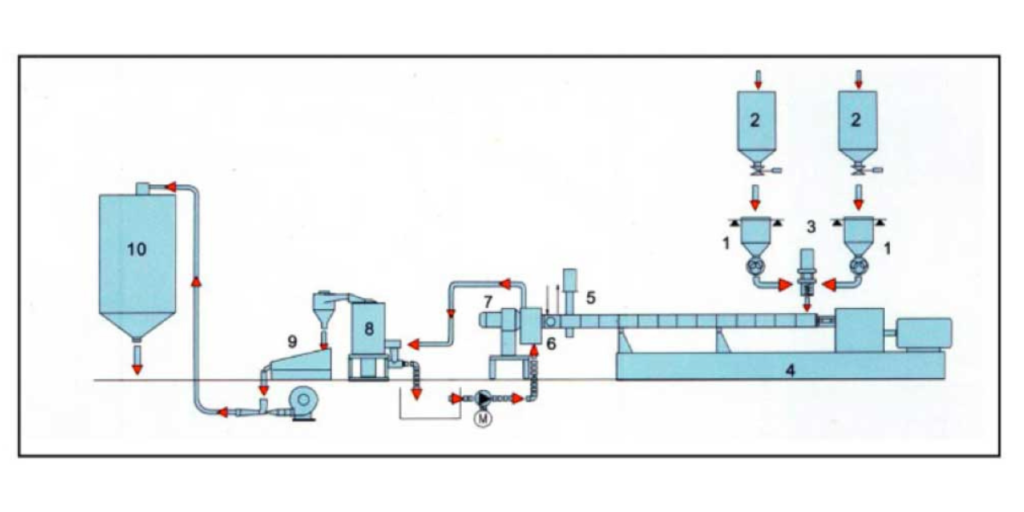
Key Benefits of Using a Twin Screw Extruder
- Effective Heat Transfer and Mixing: The twin screw design guarantees superior heat transfer and mixing, both of which are essential for obtaining reliable chemical reactions. The way the screws interlock encourages uniform shear, which makes the perfect conditions for reactions.
- Scalability: Extruders are a great option for industries that need high-volume chemical processing because they are simple to scale for large-scale production. The TSE can be adjusted to match the particular needs of the process by varying the screw speed, temperature, and pressure.
- Decreased Batch Processing Time: Traditional batch processing techniques can take a long time and frequently call for extra steps like heating and cooling. A twin extruder, on the other hand, runs constantly, cutting down on processing time and increasing output.
- Precise Control: When it comes to managing the chemical process, a twin screw extruder provides exceptional precision thanks to its ability to regulate temperature, pressure, and screw speed. Better control over the final product is made possible by this, which is crucial for producing chemicals of superior quality.
- Versatility: TSEs can be used for a variety of purposes. Polymers, food items, pharmaceutical ingredients, and even chemicals that need particular processing conditions are among the many materials they can process.
- Eco-friendly: Compared with typical batch reactors, the continuous process uses less energy and produces less waste. The process’s capacity to recycle materials also lessens its negative effects on the environment.
- Personalisation: Twin screw extruders can be made to meet the unique requirements of a given chemical reaction. To guarantee perfect reaction conditions, the extruder can be modified to add reactive agents, catalysts, or particular temperatures.
Applications of Twin Screw Extruders as Chemical Reactors
- Polymerisation: Extruders are used in the polymer industry to convert monomers into polymers. Controlling the temperature and shear forces guarantees an effective polymerisation process, producing high-quality products with reliable characteristics.
- Food Processing: Extruders are increasingly being used as continuous chemical reactors in the food industry. In order to maintain excellent quality control and efficiency, they are utilised to cook food, process ingredients, and even carry out chemical reactions like fermentation or enzymatic processing.
- Pharmaceuticals: Drug formulations and sustained-release formulations are produced in pharmaceutical manufacturing using twin screw extruders. For pharmaceutical applications, the TSE’s continuous nature is essential because it guarantees a constant product quality and minimises batch-to-batch variation.
- Bio-Chemical Production: The use of twin screw extruders in the manufacturing of bio-based chemicals and biodegradable polymers is growing. They can be incorporated into processes that generate sustainable materials by utilising biological catalysts or enzymes.
- Speciality Chemicals: The Extruder offers a high degree of supervision of the chemical reaction in the production of speciality chemicals like adhesives, coatings, and sealants, producing high-performance products with specialised properties.
- Material upcycling and reclamation e.g. recycling of polymers and reclamation rubber by devulcanization of rubber using twin screw extruder.
- Solvent recovery using twin screw extruder.
- Slurry preparation e.g. cathod and anod slurry for Lithium battery production.
- Acid and alkaline treatment e.g. sodium casienate and calsium casienate from casien and modified and pregeletinised starch from raw starch.
- Propellant grains and catalyst extrusion in desired shapes.
- Preparation of polymer composites.
Why Choose Kriimpas India Pvt. Ltd.: Dealer of Twin Screw Extruder as a Continuous Chemical Reactor
Leading the way in the supply of superior extruder systems that function as continuous chemical reactors is Kriimpas India Pvt. Ltd. Modern technology is used in the design of our products to deliver accurate, scalable, and effective chemical processing solutions. We are the best Provider of Twin Screw Extruder Machines as a Continuous Chemical Reactor.For your extruder requirements, Kriimpas India is the best option for the following reasons:
- Knowledge and Experience: Kriimpas India has years of experience producing extruders and is aware of the complexities involved in chemical processing. We create and modify our extruders to satisfy each customer’s particular requirements.
- Customisation: We provide specialised solutions at Kriimpas India. Our twin screw extruders can be tailored to your unique needs, whether you’re processing chemicals, food, polymers, or medications.
- Advanced Technology: To ensure perfect chemical reactions and constant product quality, our extruders are fitted with the newest technology for precise control over temperature, pressure, and shear forces.
- Energy Efficiency: We consider energy efficiency when designing our screw extruders. The ongoing procedure lowers waste and energy usage, making our systems both economical and ecologically friendly.
- Excellent Service and Support: We are dedicated to offering remaining customer service. Kriimpas India is dedicated to providing continuous technical support to guarantee your system runs smoothly, from the first consultation to post-installation maintenance.
- Assurance of Quality: Kriimpas India is dedicated to upholding the greatest standards of quality. To make sure they fulfil international standards and continue to operate reliably over time, our twin screw extruders are put through a rigorous testing process.
- Cost-effective Solutions: Our extruders provide a perfect ratio of affordability and performance. By offering premium, effective machinery at affordable costs, we hope to make them available to businesses of all kinds. We are the best Twin Screw Extruder Machines Dealer.
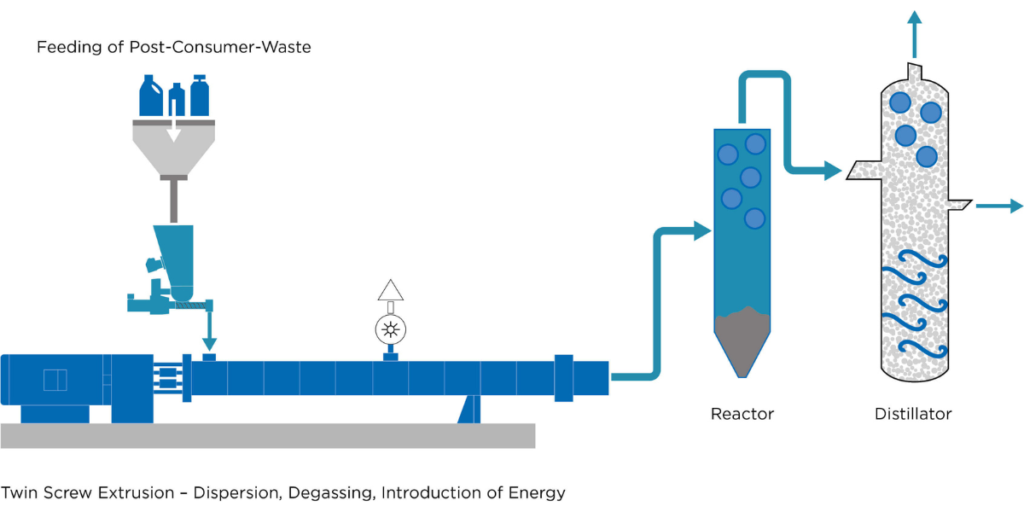
Conclusion: Dealer of Twin Screw Extruder as a Continuous Chemical Reactor
By providing an effective, scalable, and adaptable solution for chemical processing, extruders are being used as continuous chemical reactors, revolutionising a number of industries. The twin screw extruder offers a flexible platform for producing high-quality products with little waste and energy consumption by giving precise control over chemical reactions. We are the best Twin Screw Extruder Machines Provider.
We at Kriimpas India Pvt. Ltd. are pleased to provide innovative twin screw extruder systems that can be customised to meet your unique requirements and guarantee the seamless and effective operation of your chemical processing activities. Regardless of your industry—plastics, food, pharmaceuticals, or speciality chemicals—Kriimpas India is here to offer you the best business solutions.
Get in touch with Kriimpas India Pvt. Ltd. right now to find out how our twin screw extruders can improve your chemical processing activities.